Manufacturer Boosts Productivity and Workflows with Barcode Inspection Printer
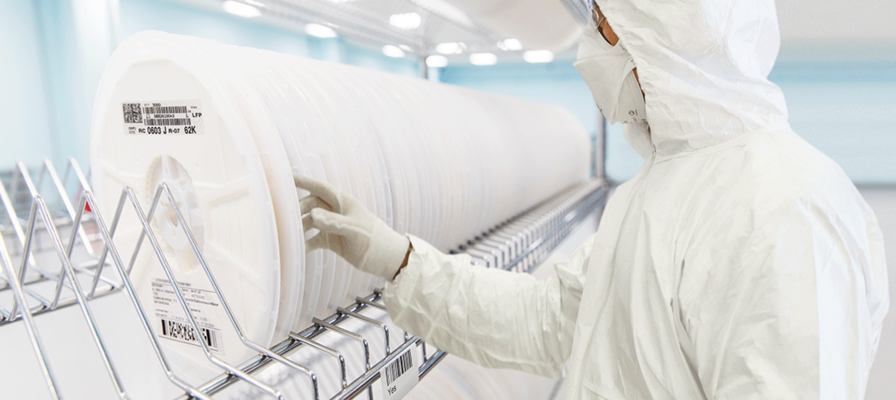
T8000 ODV-2D Achieves Zero Relabeling, Saves Up To 5 Labor Hours Per Day
Background
Order fulfillment is critical for any business. For a chip resistor, quality labels can play a critical role in productivity. In this use case, we focus on one of the world’s largest chip resistor manufactures, which has to process massive reel disks with loaded chip resistors to customers with little lead time every day. During production, the reel disks are labeled with respective part numbers. To accurately distribute reel disks to customers, a distribution identification label is applied to identify to which customer the disk should be sent.
The labeling process is highly manual and includes four labeling lines staffed with ten people each. Due to low print speed, each staff member is assigned their own printer totaling 40 printers in the production. The 40 person crew has to process more than 64,000 labels every day. Once labeled, reel disks are sent to one of two sorting lines. One line is semi-automatic where reel disks are put onto the conveyor, scanned, and then sorted into batches. The other is completely manual and handheld scanners are used to scan and sort.
Challenges
Loss of Productivity for Bad Labels
When labeling, scanning, and sorting manually, correcting unreadable labels can cause up to 5 hours of rework per day. Additionally, this causes backups on sorting lines because they are forced to stop until the labels are corrected. During the rework process, staff needs to rescan the part number label, print a new identification label, and scan and sort again for packing. It is estimated that 1% of the labels will need to go through this process. That means 640 labels corrected each day, which reduces productivity by 21% each day. To prevent this, the resistor manufacturer sought out a solution to verify and validate barcodes to ensure print quality at the point of label creation. Their criteria included:
- Any unqualified, unreadable, or bad labels can be identified and corrected before labeling
- Print speed up to 6 inches per second (ips)
- Reliable for 24/7 operation (3 shifts a day)
Solution
Inspect Every 1D and 2D Barcode at the Point of Creation
The manufacturer evaluated two options. One was a system-integrator-built solution. The second option was TSC Printronix Auto ID’s T8000 ODV-2D printer, an all-in-one solution that enables the manufacturer to print, scan, verify, and validate 1D and 2D barcodes in a single print job.
The robust T8000 ODV-2D barcode inspection printer includes a built-in barcode verifier that grades and validates barcodes to ISO standards. The fully automated T8000 ODV-2D can also overstrike bad labels and reprint a new one without operator intervention.
The T8000 is much more efficient than other inspection solutions that identify any unqualified barcodes, as the print process has to stop and requires manual reprint. Additionally, the bad label isn’t destroyed, which leaves room for human error. Staff could feasibly place the incorrect label on a reel disk.
Figure 1: The T8000 ODV-2D printer does not require any operator intervention. It enables you to print, validate, verify, overstrike and reprint labels in a single pass.
Why Choose TSC Printronix Auto ID?
TSC Printronix Auto ID’s T8000 ODV-2D printer represents a fully-integrated solution that requires zero intervention in the process to print, scan, verify, validate, overstrike, and reprint labels. The print speed of the T8000 ODV-2D is up to 8 ips, which is much faster than previous desktop printers. One T8000 ODV-2D printer can cover the previous workload of 10 printers. The manufacturer now only needs four T8000 ODV-2D printers to fulfill their daily heavy print demands—this is compared to 40 printers in their previous process which used 10 times as many! The T8000 solution’s simplicity provided better value and greater savings than the manufacturer expected, providing them with an excellent ROI.
Option 1 | Option 2 |
---|---|
System-Integrator-Built Solution | TSC Printronix Auto ID’s T8000 ODV-2D |
Consists of three elements: an industrial printer, an external 2D scan module, and label verification technology software. | All-in-one solution: able to print, scan, verify, and validate in one process. |
|
|
Table 1. Two Option Comparison
During a three month trial period, the T8000 ODV-2D printer worked under 24/7 operation to prove its true reliability and durability. During that time, TSC Printronix Auto ID was quick to respond to the needs of the customer and provided support as needed. All issues are received by our support team and resolved quickly minimizing operational delays.
Adopting the T8000 ODV-2D resulted in a zero label defect rate, no more relabeling, and no more labor waste in their processes. The issue was solved—internal workflow was improved while also saving time and labor. The T8000 ODV-2D printer provided a significant cost, labor, and efficiency savings for this manufacturer.
Figure 2: Before and After the T8000 ODV-2D Deployment